Having Full Control
We design with manufacturing in mind, creating a unique and seamless integration of both. We operate a dedicated workshop where new processes are meticulously planned and tested before going into full production. Our commitment to understand the entire manufacturing process ensures that we maintain full control - from inception to completion.
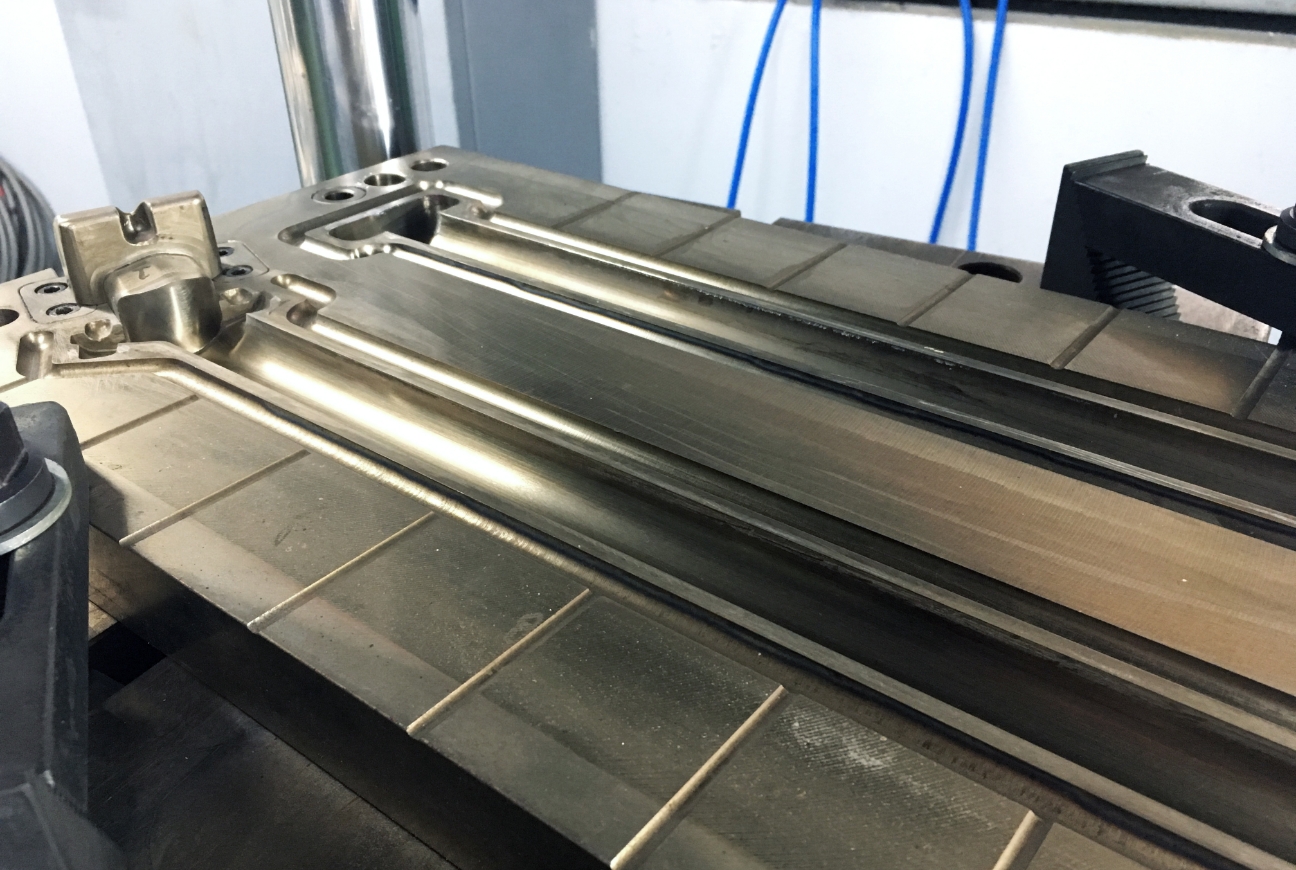
Holistic Design Processes
Our holistic approach ensures that our components meet the highest standards. We utilize computer-simulated Finite Element Analysis (FEA) to predict how components will react to real-world forces, as well as Laminate Tools, enabling our engineers to map plies of carbon directly over the virtual model.
And we don’t stop there. By designing with manufacturing in mind, we optimize the production process to ensure efficiency and innovation. Often, this leads to developing entirely new manufacturing methods. Our workshop serves as a test kitchen where we refine the entire process: we create our own tools, layups, and cutouts, along with auxiliary devices such as cores and layup tools. This holistic approach allows us to seamlessly integrate design and production, resulting in superior performance and reliability of our components.
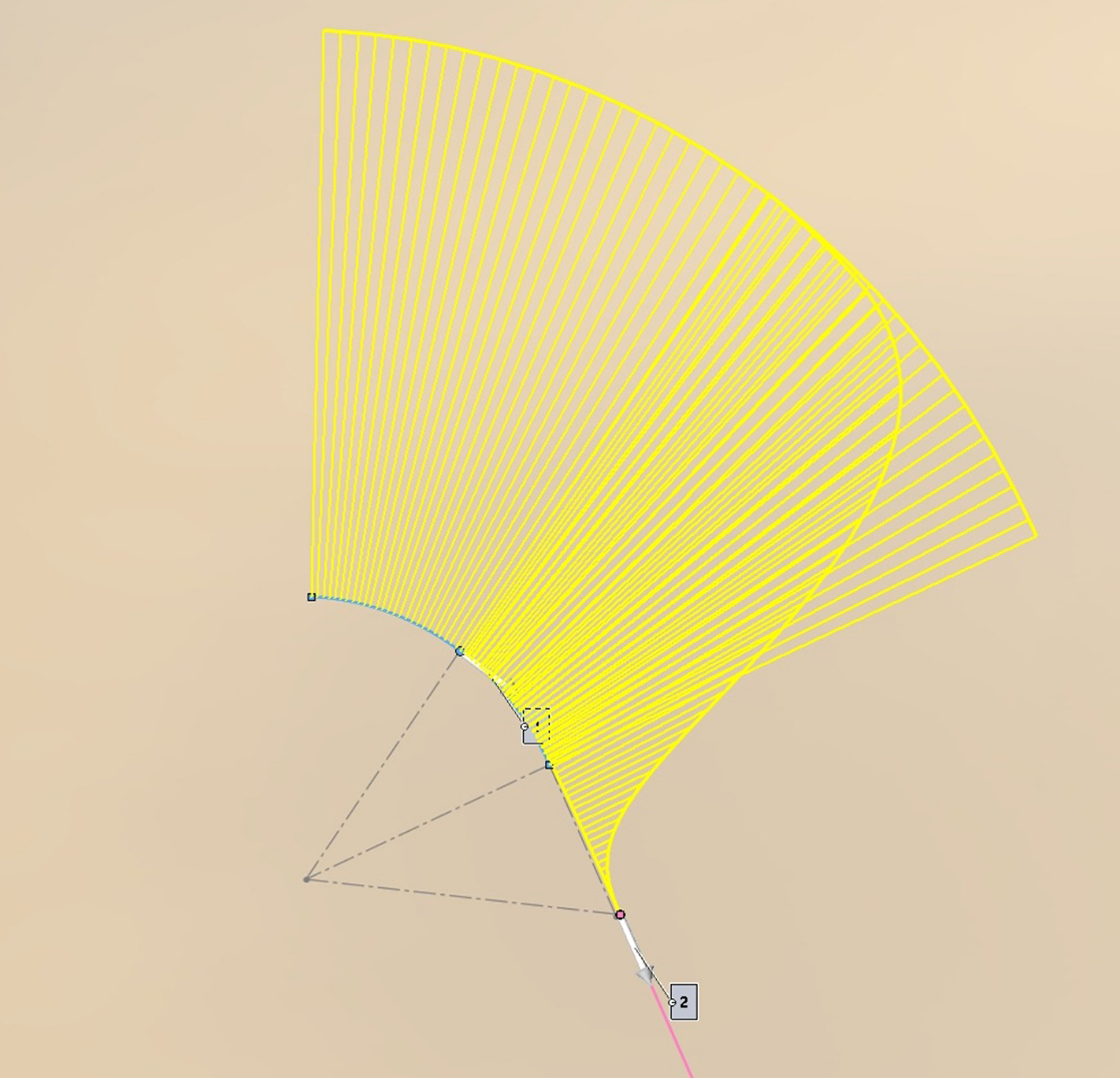
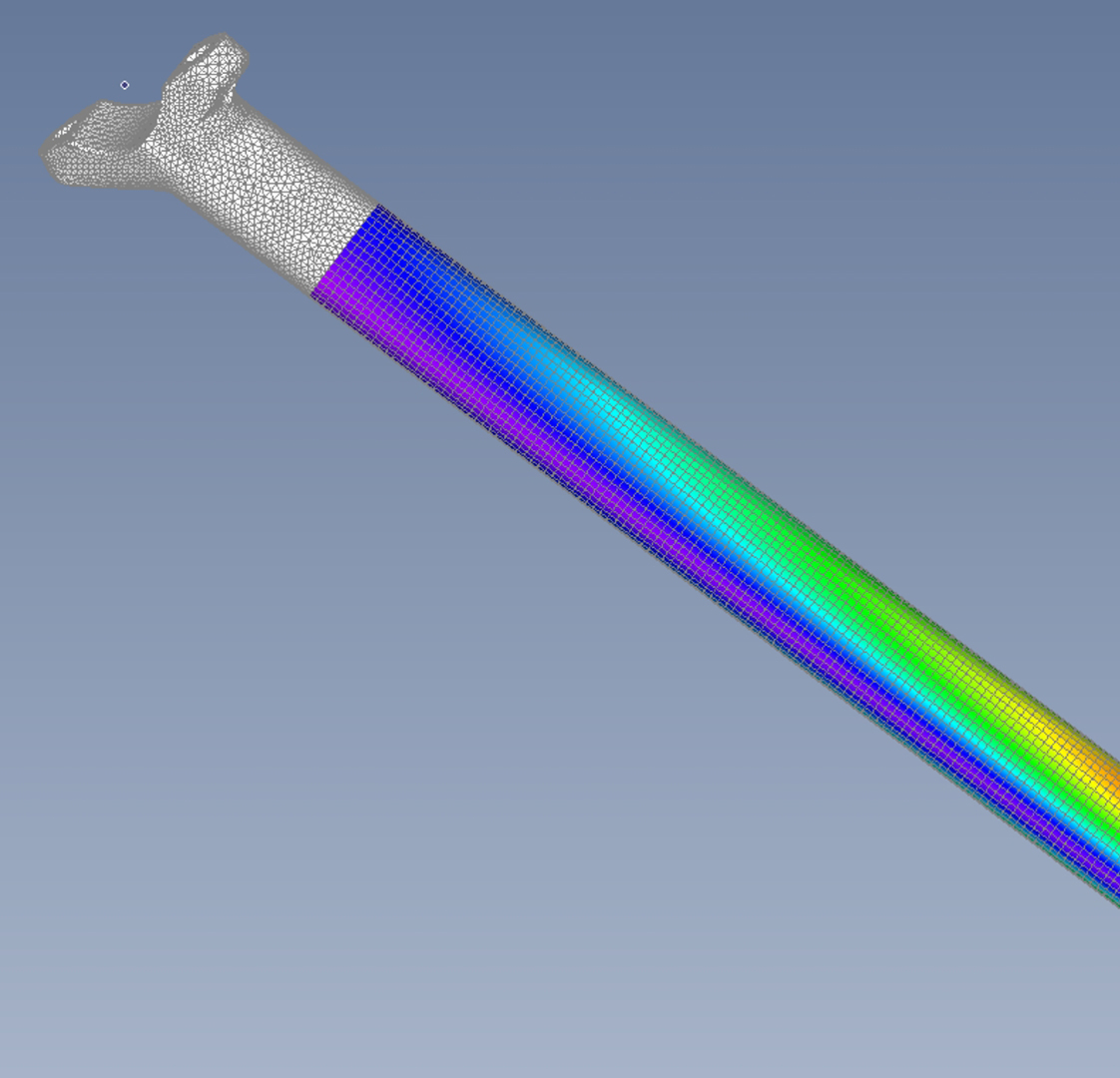
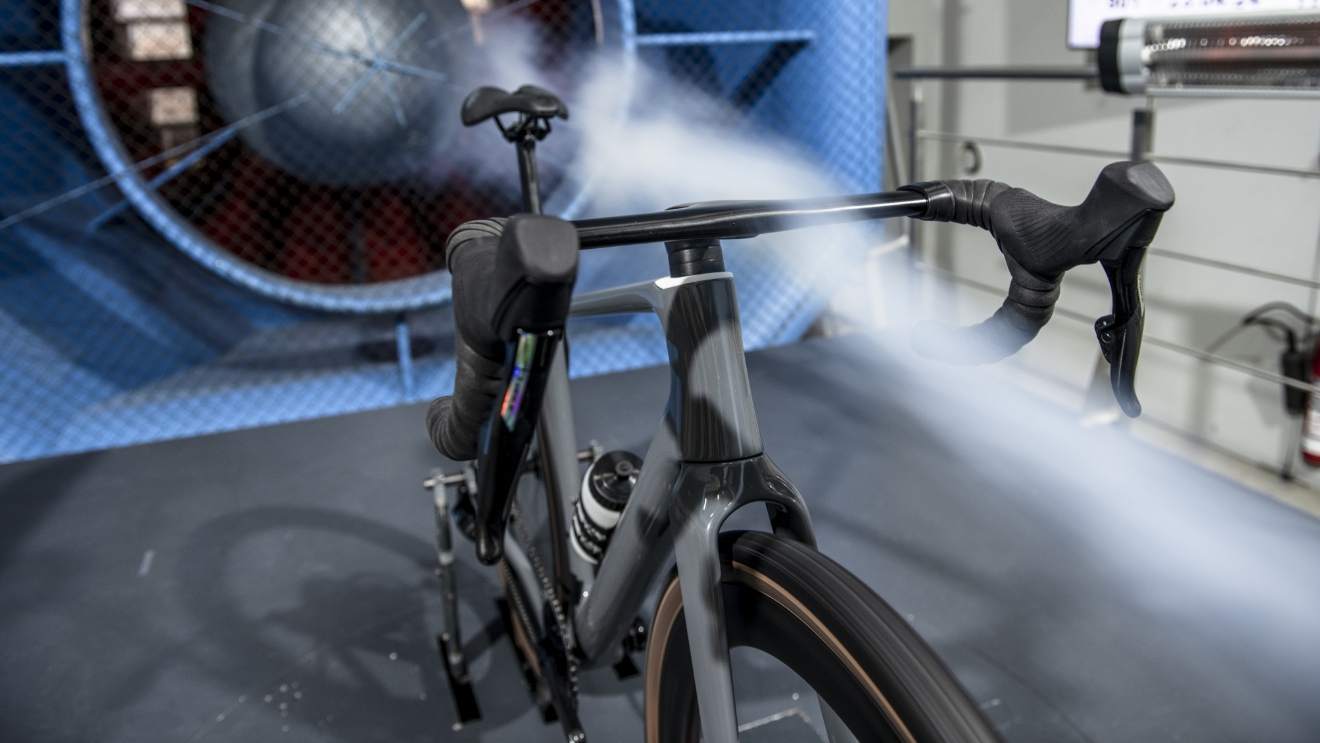
Pioneering manufacturing…
3D Forged Carbon (3DFC)
For hollow but complex shapes, we use a process we developed called 3DFC (3D Forged Carbon). We were the first to pioneer this unique manufacturing method, pushing the limits of what is feasible. This technique combines the high-pressure CPMC technique with traditional long fiber carbon plies, all in one step for optimal performance. The result is our Wuthocker, the world's first one-piece 3D-forged carbon seat post which is a showcase of Faserwerk’s unique DNA: optimizing designs to create parts that not only perform exceptionally but are also manufactured in the most efficient way.
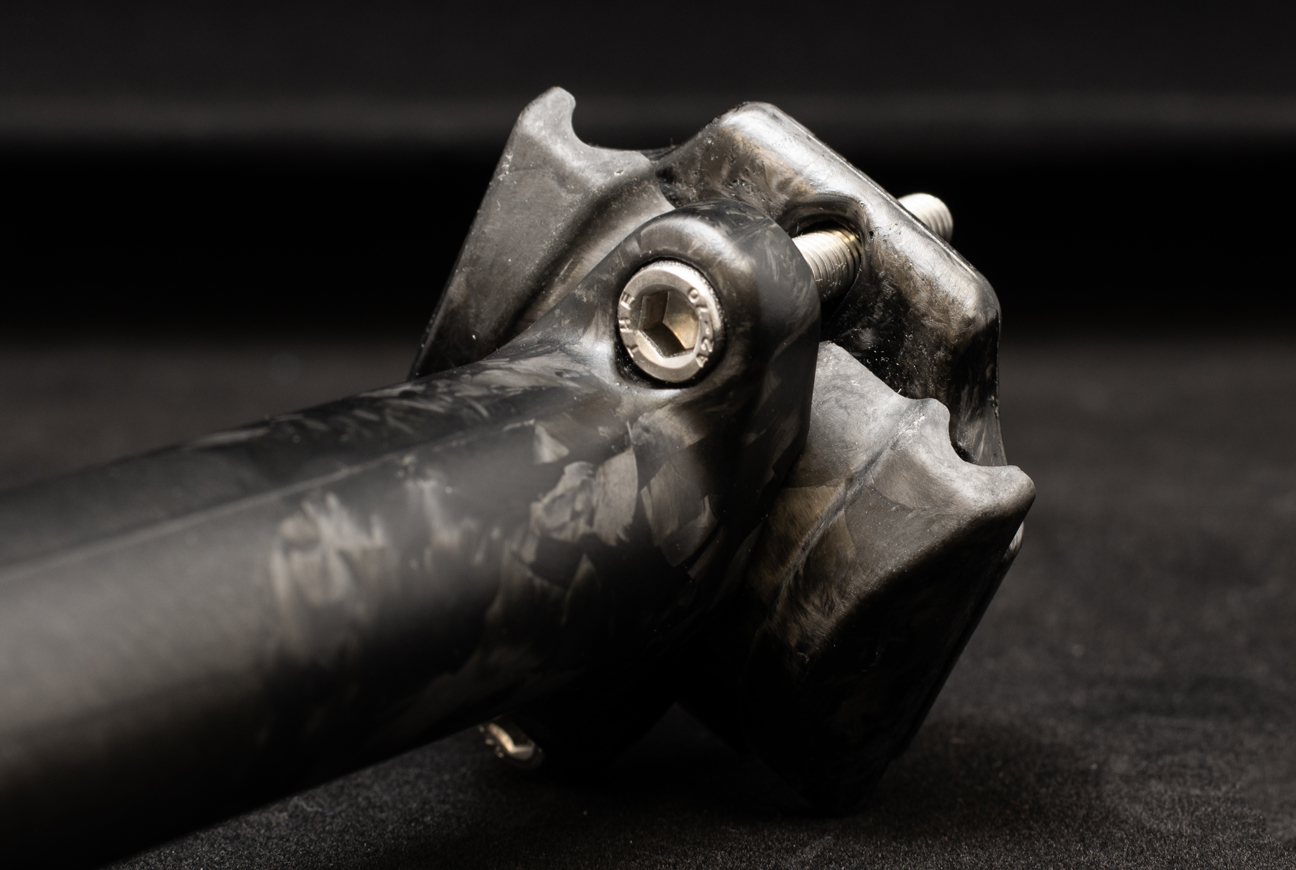
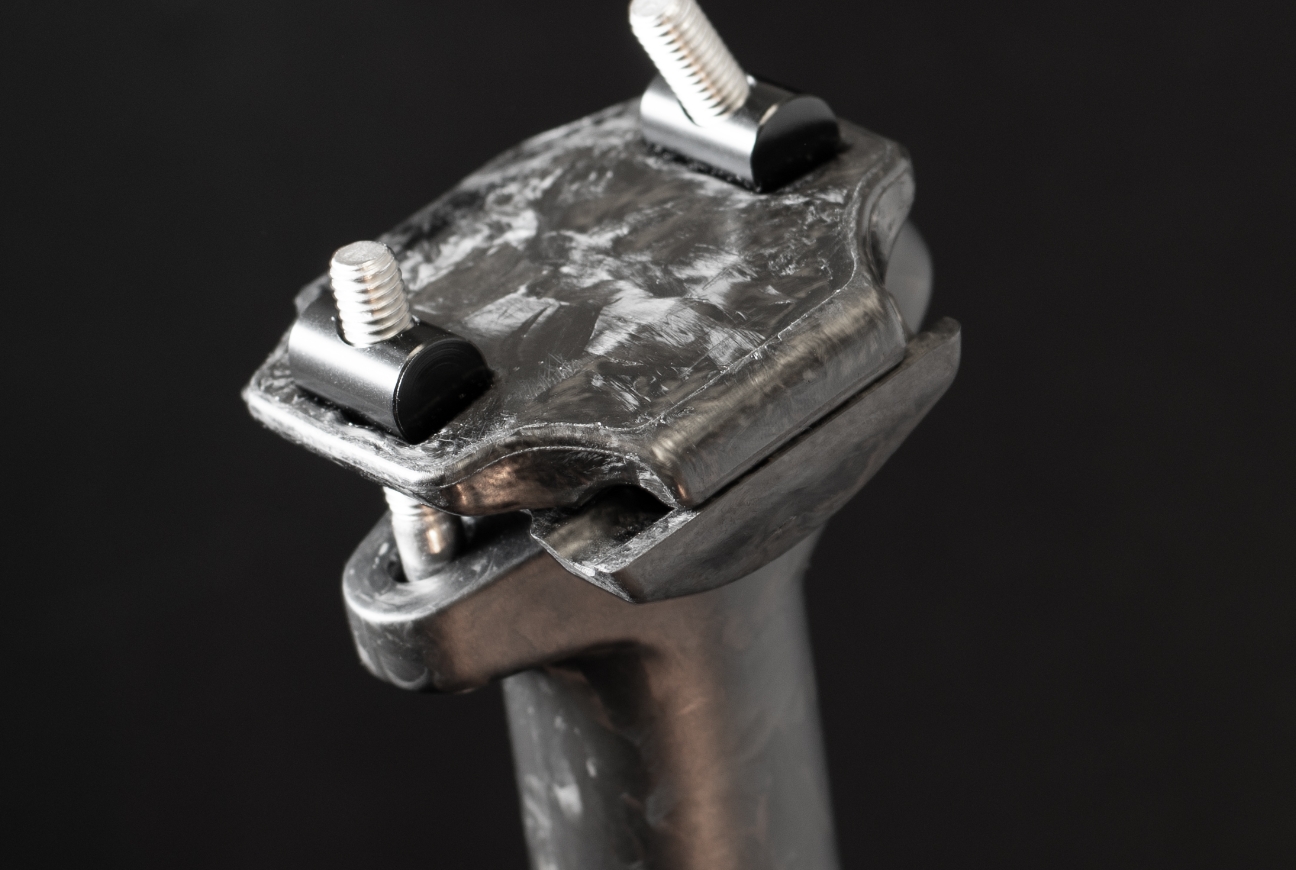
…with rider benefit in mind.
Viscoelastic Damping
Rider comfort is paramount, and we recognize that it can never be left out of the equation. To enhance comfort without compromising on weight or performance, we developed the first handlebar on the market featuring a strategically placed viscoelastic damping layer between stiff carbon fibers. This innovation results in a handlebar that is not only extremely lightweight but also significantly reduces rider fatigue.
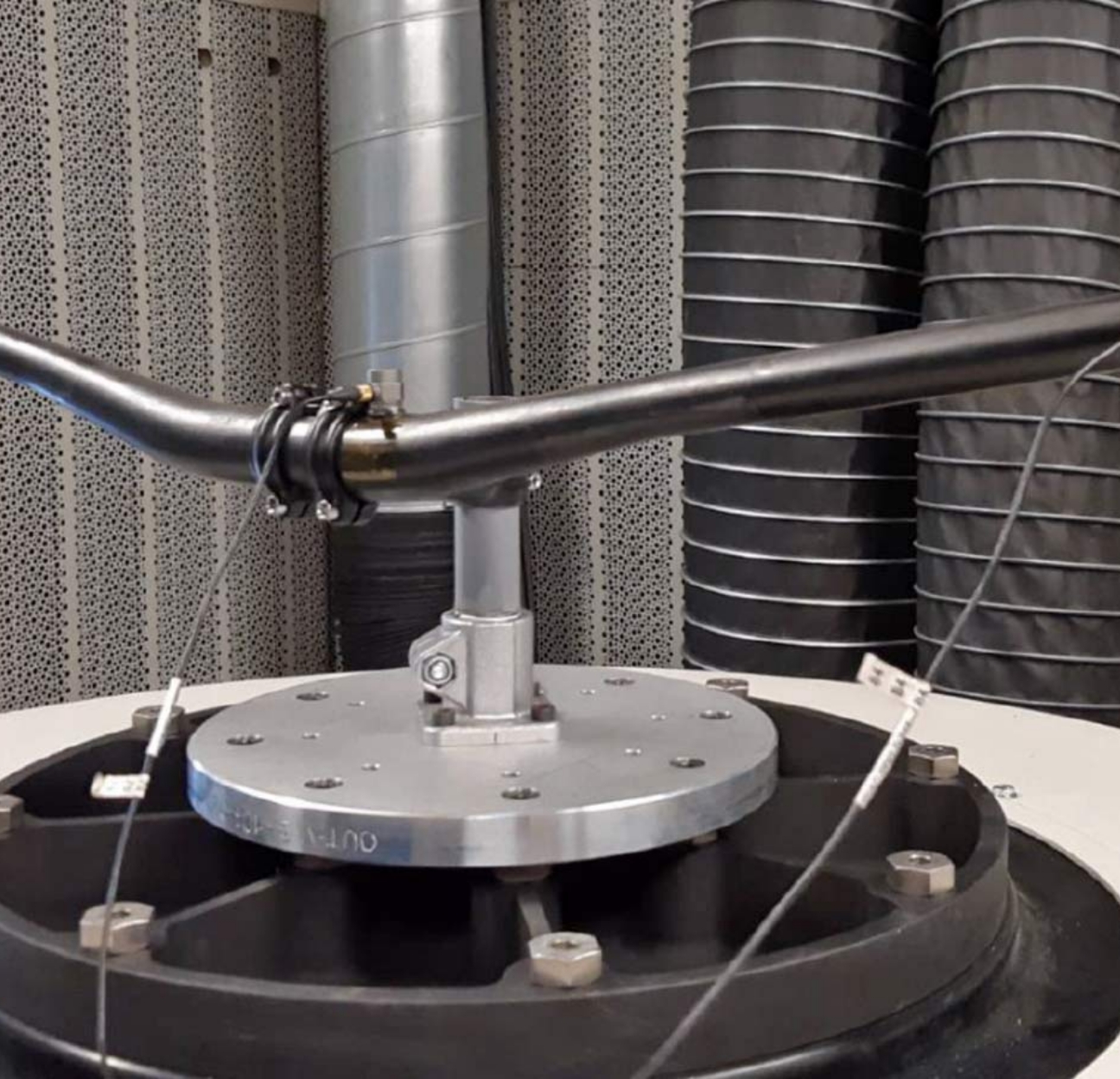
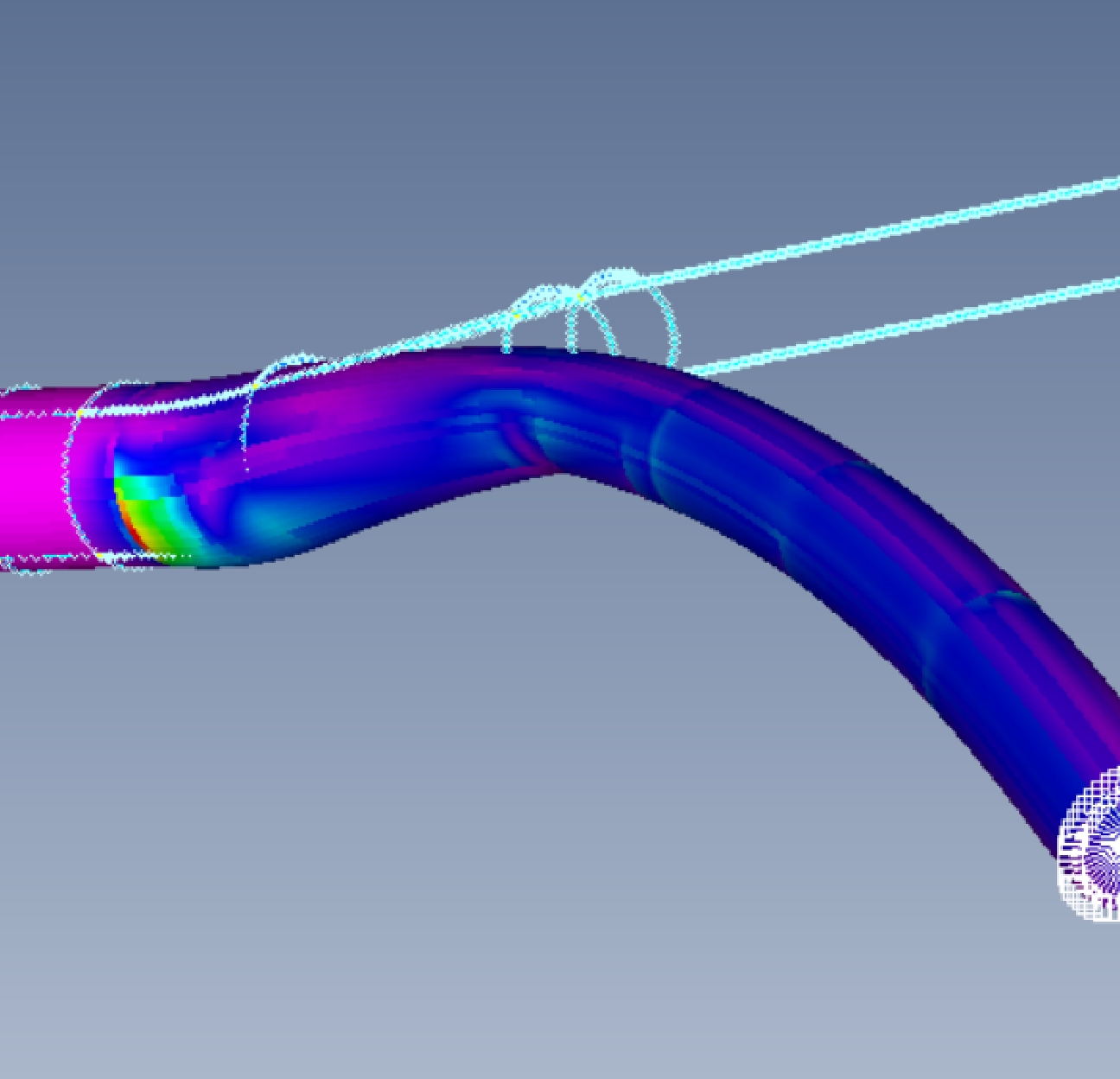
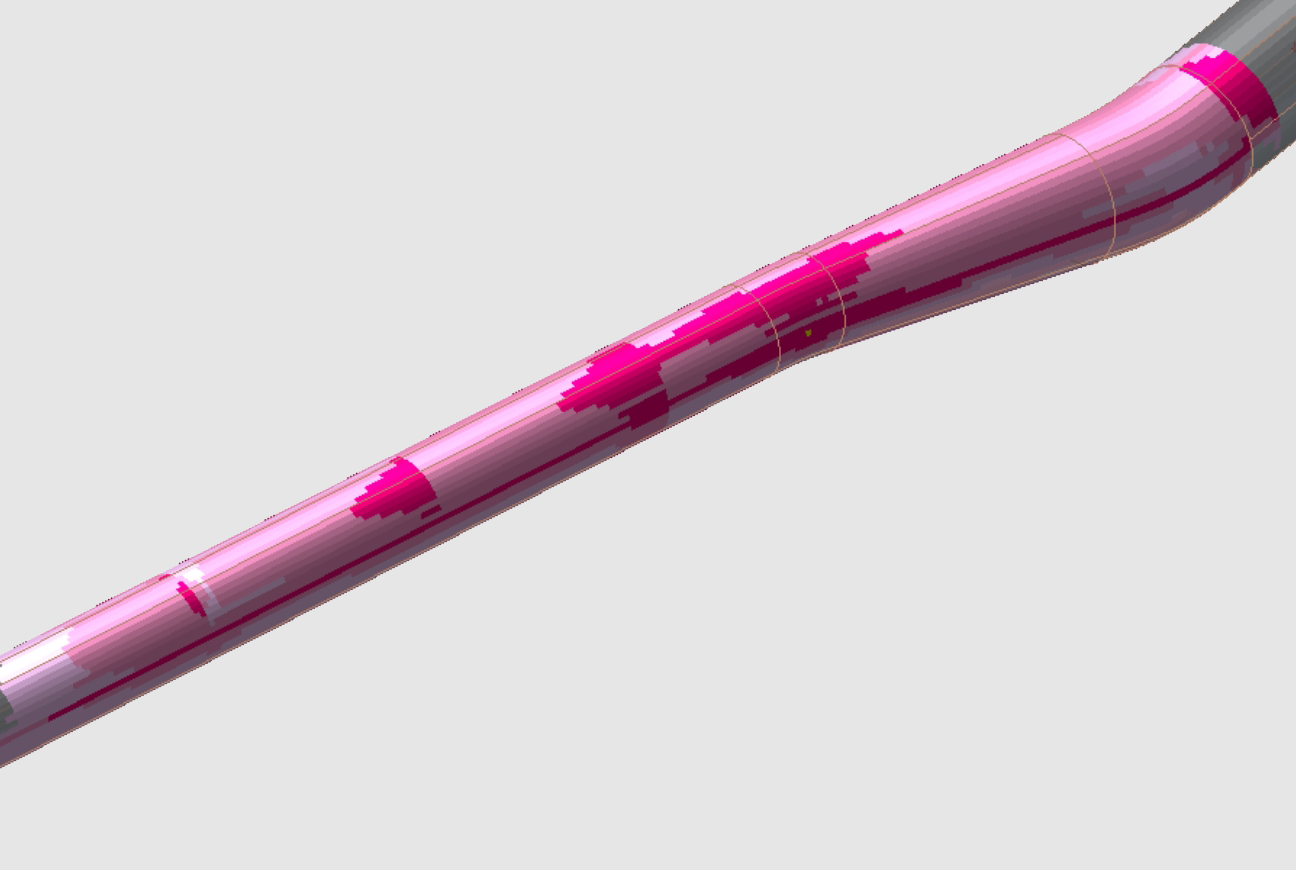
Compression Molding Compound (CPMC)
CPMC enables us to efficiently mold complex carbon parts under extremely high pressure. This technique is similar to forging but uses carbon. We use CPMC to create the hardware on top for saddle rails. The high pressure compacts the carbon fibers tightly, resulting in parts with excellent strength and quality right out of the mold. This enhances durability and reliability, ensuring that the saddle rails maintain their integrity even under the most demanding conditions.
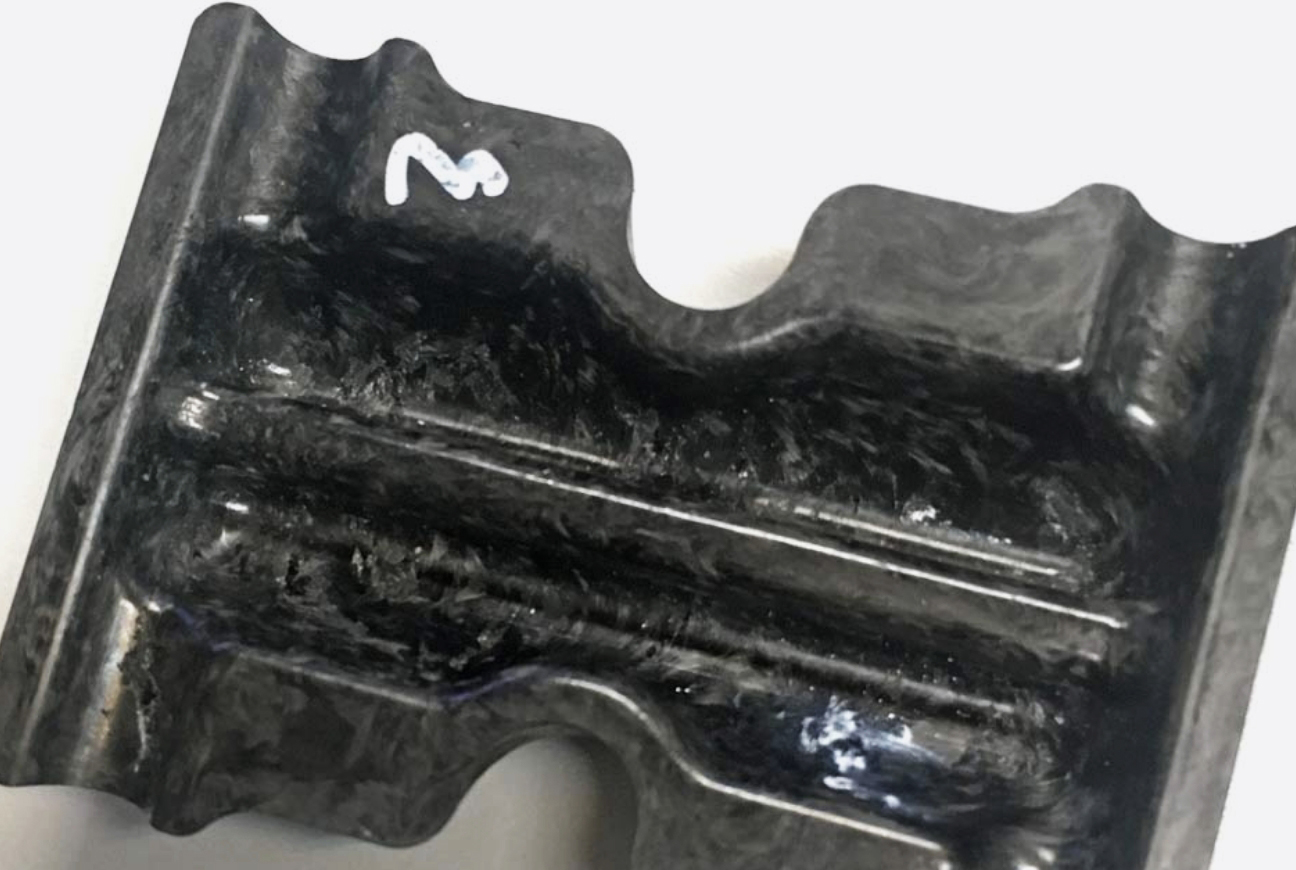
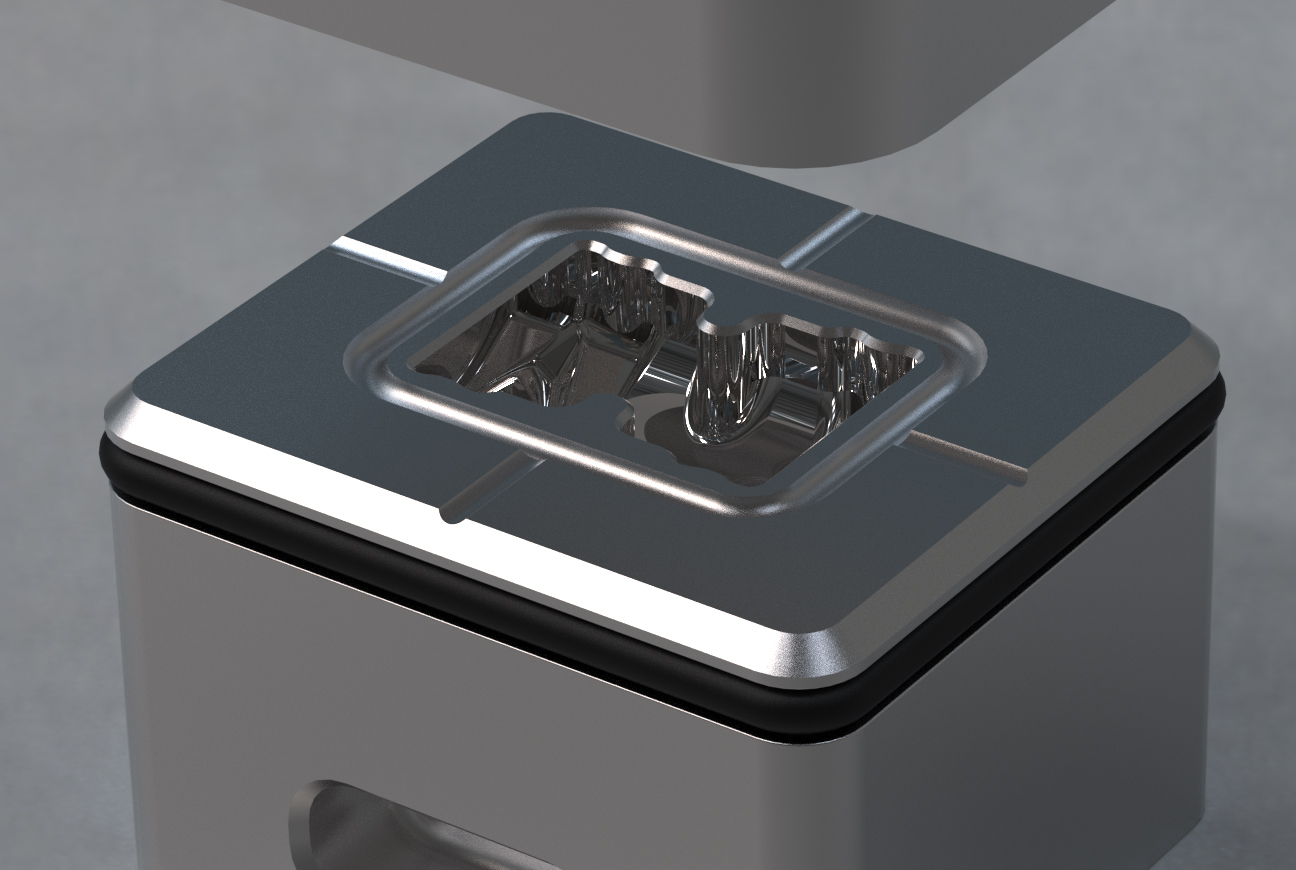
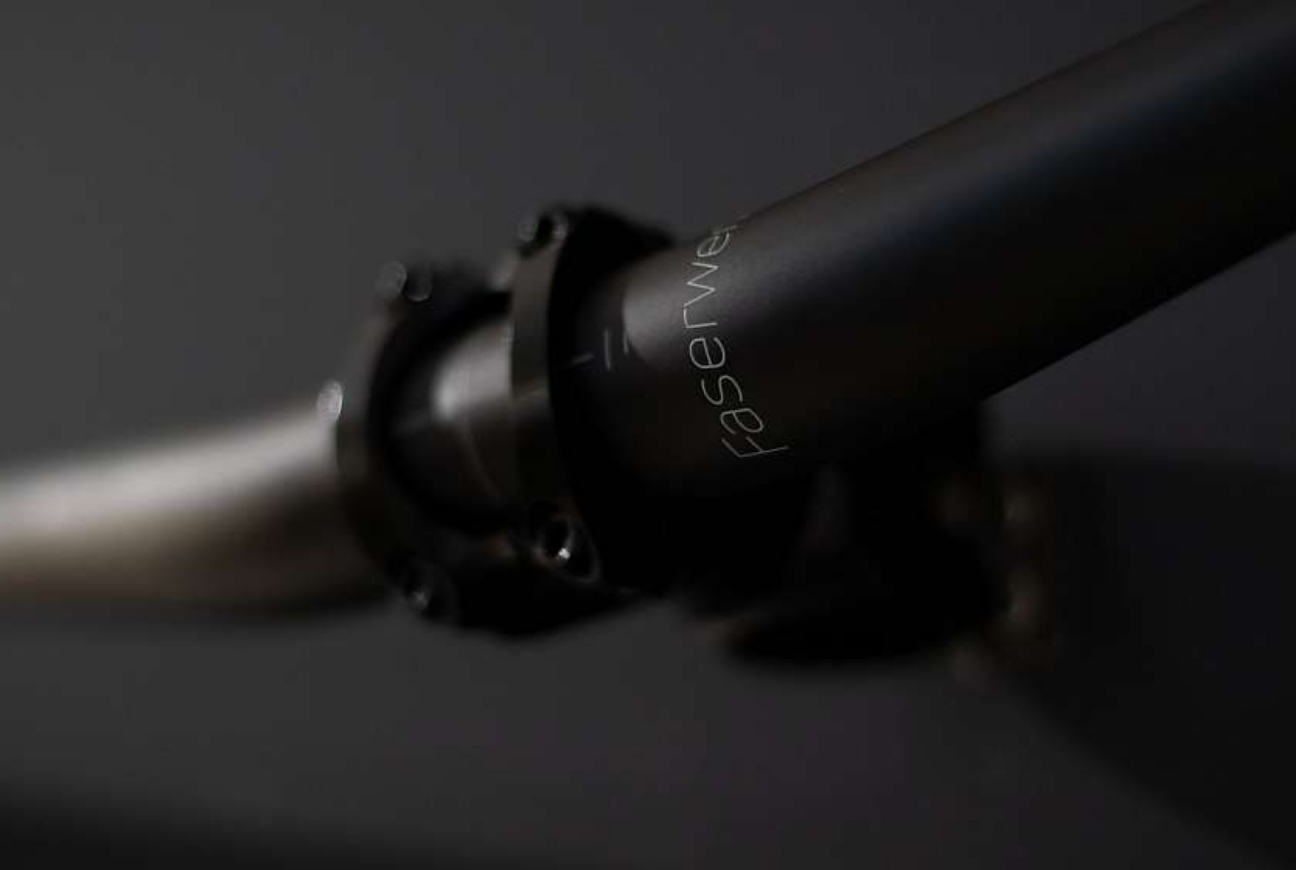
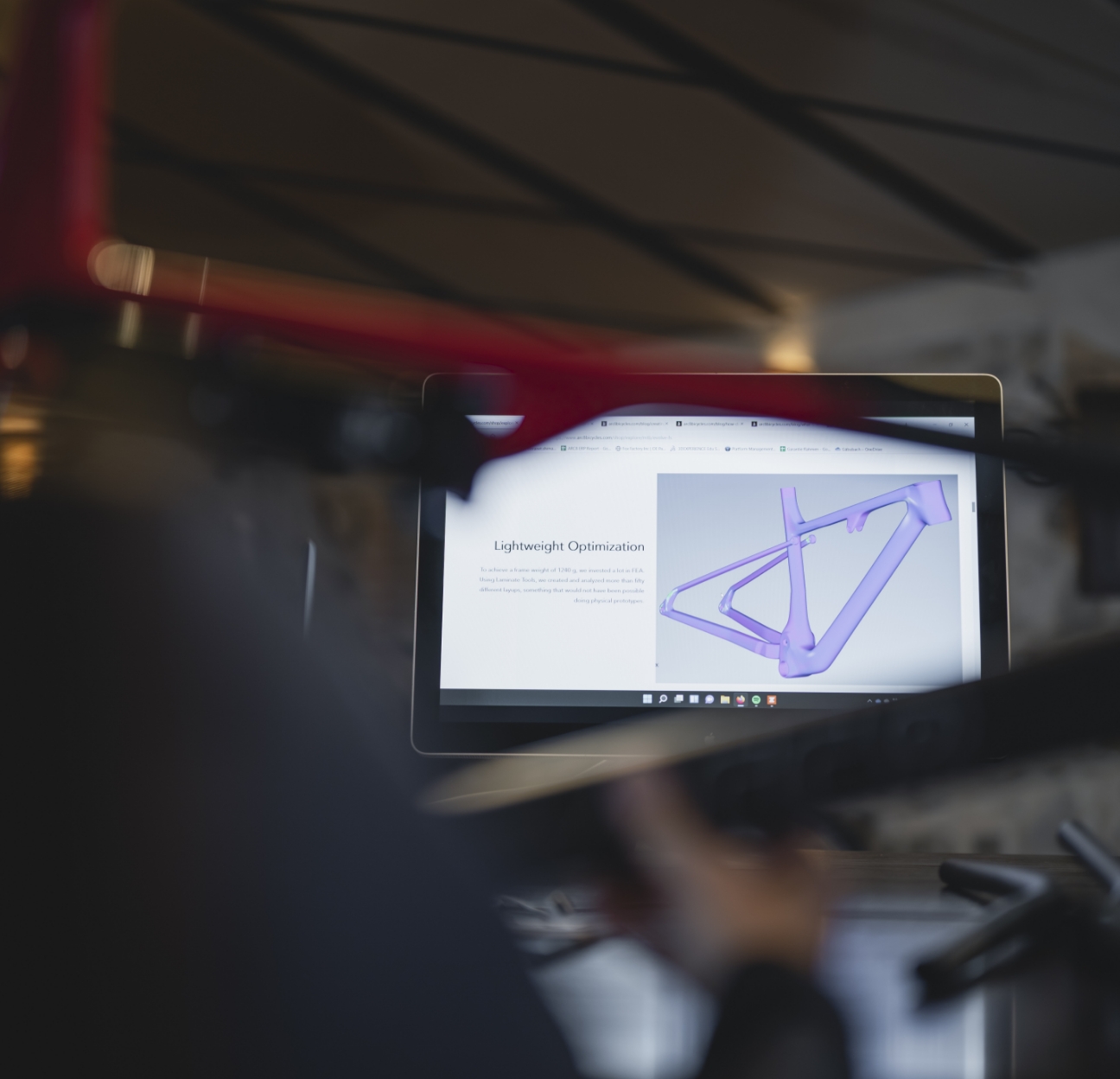

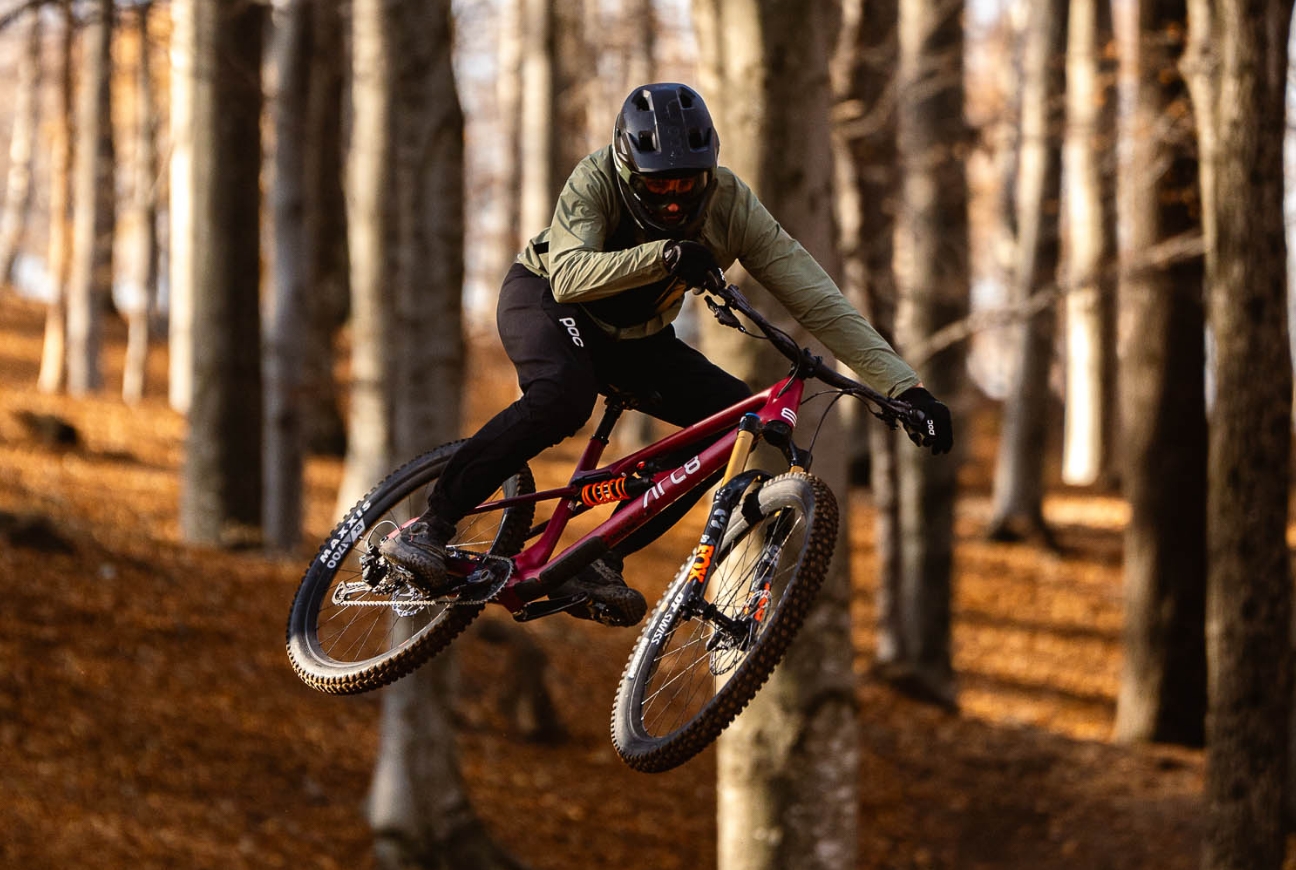
"At Faserwerk, our mission is to push the boundaries of bike component design by seamlessly integrating engineering and manufacturing. This holistic approach ensures that every part we create delivers the highest level of performance, reliability, and rider comfort."
Jonas Müller